Kami memberikan solusi khusus kepada semua pelanggan kami dan menawarkan saran teknis lengkap yang dapat dimanfaatkan oleh perusahaan Anda.
Cetakan injeksi adalah proses manufaktur di mana suatu bahan, biasanya plastik, dilebur dan disuntikkan oleh mesin ke dalam cetakan. Itu sekrup di mesin cetak injeksi membantu memanaskan dan mengangkut bahan yang meleleh ke dalam cetakan. Desain sekrup merupakan faktor penting dalam efisiensi dan kualitas proses pencetakan injeksi.
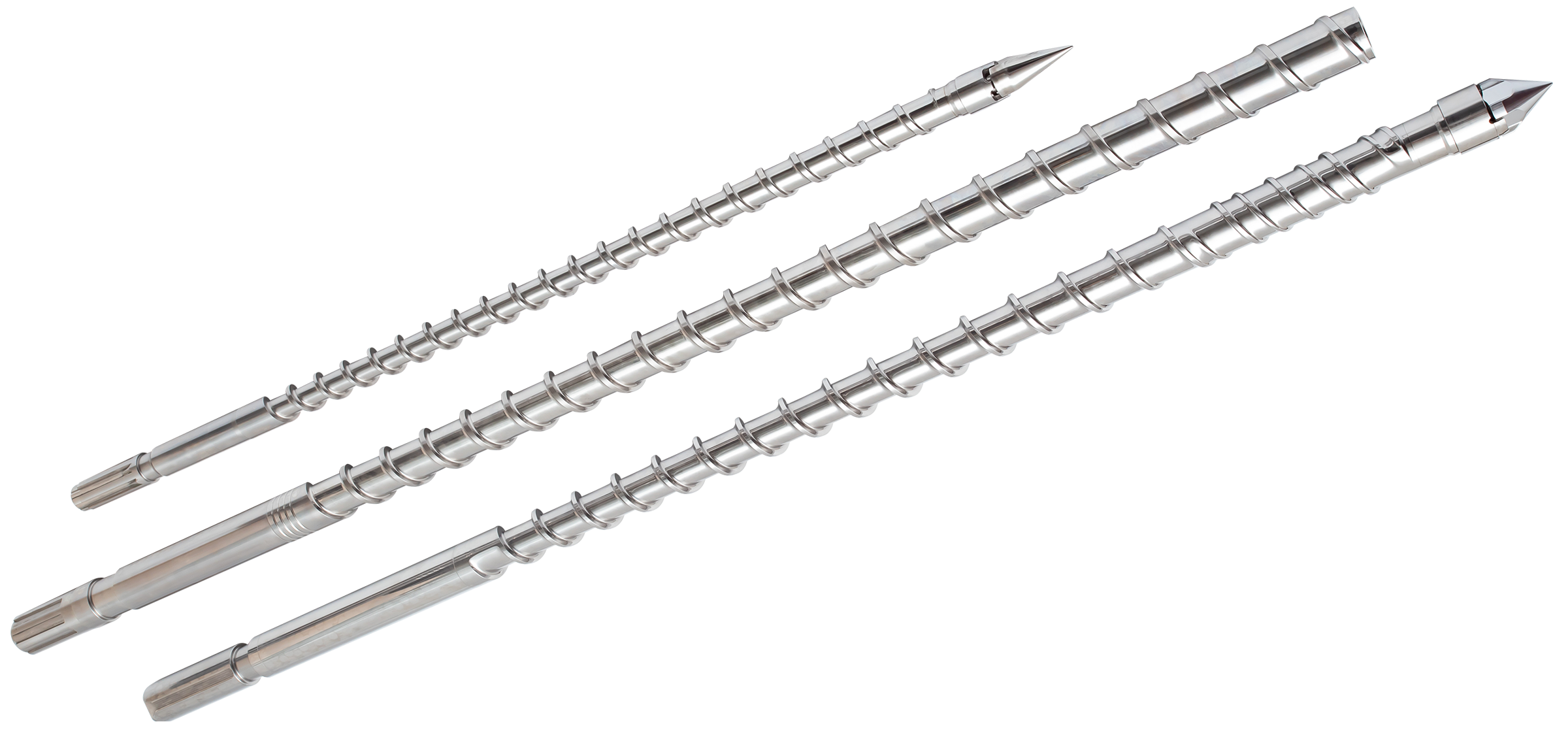
Ada beberapa faktor yang perlu dipertimbangkan ketika merancang sekrup cetakan injeksi:
1. Bahan: Jenis bahan yang dicetak akan mempengaruhi desain sekrup. Bahan yang berbeda memiliki suhu leleh dan sifat aliran yang berbeda, dan sekrup harus dirancang untuk menangani sifat ini secara efektif.
2. Suhu pemrosesan: Suhu pemrosesan mengacu pada suhu saat bahan disuntikkan ke dalam cetakan. Sekrup harus mampu mempertahankan suhu ini saat mengangkut material melalui mesin.
3. Tekanan: Tekanan saat material disuntikkan ke dalam cetakan akan mempengaruhi desain sekrup. Tekanan yang lebih tinggi dapat digunakan untuk mengisi cetakan lebih cepat, namun juga dapat menyebabkan material rusak atau menimbulkan masalah lain jika tidak dikontrol dengan hati-hati.
4. Waktu tinggal: Waktu tinggal mengacu pada jumlah waktu yang dihabiskan material di dalam tong mesin cetak injeksi. Sekrup harus dirancang untuk mengoptimalkan waktu tinggal untuk memastikan bahwa material benar-benar meleleh dan homogen sebelum disuntikkan ke dalam cetakan.
5. Peleburan dan pencampuran: Sekrup harus dirancang untuk melelehkan dan mencampur material secara efektif saat diangkut melalui laras mesin. Hal ini biasanya dicapai melalui penggunaan geometri sekrup dan konfigurasi penerbangan tertentu.
Desain sekrup cetakan injeksi PVC
PVC (polivinil klorida) merupakan bahan plastik yang umum digunakan dalam cetakan injeksi. Ia memiliki kekuatan, kekakuan, dan ketahanan cuaca yang baik, serta dapat dengan mudah dibentuk menjadi berbagai bentuk dan produk.
Saat merancang sekrup untuk cetakan injeksi PVC, ada beberapa faktor yang perlu dipertimbangkan:
1. Suhu leleh: PVC memiliki suhu leleh sekitar 220-270°C, tergantung pada formulasi spesifiknya. Sekrup harus mampu mempertahankan suhu ini saat mengangkut material melalui mesin.
2. Waktu tinggal: PVC memiliki suhu leleh yang relatif rendah dan dapat terdegradasi jika menghabiskan terlalu banyak waktu di dalam tong mesin cetak injeksi. Sekrup harus dirancang untuk mengoptimalkan waktu tinggal untuk memastikan bahwa material benar-benar meleleh dan homogen sebelum disuntikkan ke dalam cetakan.
3. Pencampuran: PVC memiliki kecenderungan untuk memisahkan, atau memisahkan, selama proses pencetakan injeksi. Sekrup harus dirancang untuk mencampur material secara efektif saat diangkut melalui laras mesin untuk memastikan produk akhir yang seragam.
4. Tekanan: PVC memiliki titik leleh yang relatif rendah, sehingga biasanya disuntikkan pada tekanan yang lebih rendah dibandingkan bahan lainnya. Sekrup harus dirancang untuk menghasilkan tingkat tekanan yang sesuai untuk mengisi cetakan secara efektif tanpa menyebabkan kerusakan material.
Singkatnya, desain sekrup cetakan injeksi merupakan faktor penting dalam efisiensi dan kualitas proses pencetakan injeksi. Ini harus dirancang secara hati-hati untuk menangani sifat spesifik dari bahan yang dicetak dan untuk mengoptimalkan berbagai parameter proses.